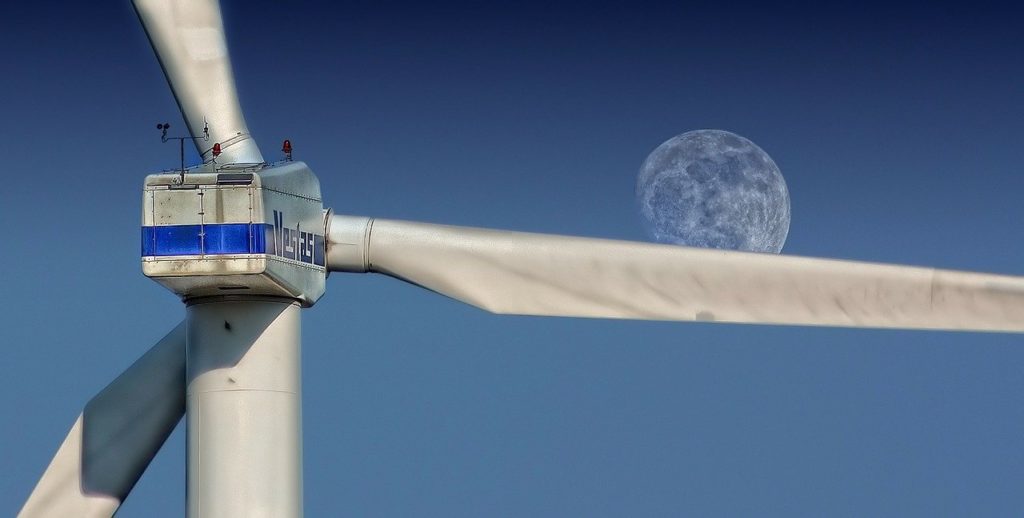
Renewables are coming to the fore and wind energy is getting a close look in the Gulf. But where will the parts for the turbines come – from New Orleans.
An uptick in demand from manufacturers looking to supply turbines for wind farms popping up around the globe is driving an expansion at Advanced Cutting Solutions. The New Orleans-based company is investing $750,000 over the next two years for at least two more machines that it uses to make wind turbine blade kits — the building blocks used by manufacturers to assemble turbines for wind farms. The company expects to hire two dozen workers to run the machines to meet growing demand. Renewable energy projects have increased as customers of utilities have demanded less carbon intensive ways to power homes and vehicles, while many nations, states, cities and businesses have committed to reducing greenhouse gases by 2050. “We create the bones of the turbine blades themselves,” said Peter Schneeweiss, co-founder and vice president and director of business development at Advanced Cutting Solutions, incorporated in 2014.
nola.com
And these “bones” are large! According to the U.S. Energy Information Administration, in 2016 the average height of a wind turbine was 280 feet. By 2017 the off shore wind farms had heights of 466 feet, , according to estimates by a researcher at the Lawrence Berkeley National Laboratory. At the first off shore wind farm off Block Island, the turbines were 590 feet with 100 foot blades. Yes they are large!
Typically, manufacturers contract with Advanced Cutting Solutions and send along 3D-scanned models of the wind turbine blade mold surface. The company then builds a prototype before completing the order. The wind turbine blade bones can be made of a variety of materials, such as PET foam, which is recycled plastic, PVC or even balsa wood that is largely harvested from trees in Latin America. Whichever materials are used as the core, it is wrapped in fiberglass during the manufacturing process. “We cut those (bones) into puzzle pieces, like one through 1,000, and then turbine manufacturers assemble the puzzle” along the inside of the hull of a wind turbine blade, Schneeweiss said. The company was co-founded by Schneeweiss and Nathanial Makin and has grown to roughly 75 workers, ranging from operators to engineers. Makin, president of the company, worked as an engineer for Schlumberger in the New Orleans area for several years before the pair began the venture. Schneeweis hails from New York state and previously worked in sales for Eastman Machine Co.
Wind turbine kits are the main construction part but the company is also looking at the marine industry maritime facility companies as the can make kits with fiberglass and carbon fiber. Starting out with small companies the number of kits was corresponding low. Moving into larger companies they now can construct 72 blade kits a week and are ramping up to reach 100 per week.
It grew from 3,000 square feet to 27,000 square feet by 2020. Last year, the company leased a new building in New Orleans East that’s about 38,000 square feet and has been customized for the business. It is inside the Michoud Assembly Facility, the former NASA site. “We did an entire build-out over the last year,” Schneeweiss said. The company has an internal formal three-month training apprenticeship-style program. It pays operators state industry averages hourly and offers health insurance benefits along with a 401(k) plan. “We really hired a lot of people without (specialized) skills, mainly people who are hardworking who we can trust and are reliable, willing to learn,” he said. “We’ve trained almost everybody from within. It’s a totally new industry.”
Demand has begun building over the past 5 years and the company hopes to expand and reach more companies asking for more contracts.
“There’s a bigger push now, and our customers are looking to build more blades because their customers are looking for blades,” he said. “We really put our attention to how we can get greater efficiencies for raw materials to make (wind turbine blades) more efficient. Back in the beginning, people were building these kits by hand, but one of the things that separates us is that it’s automated, consistent and a reliable part every time it comes out. Customers have a more efficient kit because it’s the same kit.” “We would like to expand our footprint here in New Orleans and nationwide and possibly globally,” Schneeweiss said. “We’d like to expand (back) into other industries, such as transportation and aerospace.” In exchange for its expansion investment, the company is seeking an Industrial Tax Exemption Program incentive from the state and from local government entities that would be an 80% break on property taxes over 10 years. It also has applied for the state Enterprise Zone program, which is a tax credit of either $3,500 one-time or $1,000 for each new job, in addition to a rebate of state sales and use taxes on materials such as machinery or equipment or 1.5% refundable investment tax credit on the total value of the capital investment. Businesses must create at least five jobs in an Enterprise Zone or certify that at least half of its employees live in a historically disadvantaged neighborhood or have received public assistance.
It shows that money and jobs can be made in renewable energy and this company is on the ground floor for the wind energy option.